Continuous Galvanizing
The advantages of continuous galvanizing
At Gregory Industries, we take pride in our continuous galvanizing process because it represents the continuity of our family, our team and our partnerships. When steel is coated using continuous galvanizing, the resulting products perform better and last longer.
Read on to learn more about the benefits of continuous galvanizing or contact a member of our team to request a quote today.
YOUR GALVANIZING OPTIONS
Galvanized steel is commercially coated by either the batch dip or continuous method. While either process is capable of producing a product that meets technical specifications, the coating processes produce significant metallurgical differences in the structure and characteristics of the galvanized coating.
Toggle below to learn more about each approach.
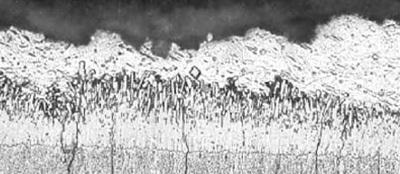
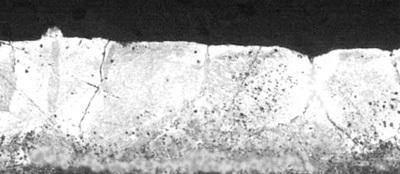
Top benefits of continuous galvanizing
More durable coating structures
Iron-zinc alloy layers make up about half of the coating resulting from batch galvanizing. With continuous galvanizing, the coating consists of virtually 100% free zinc with only a sub-microscopic alloy bonding layer. The thicker free zinc layer helps to increase part performance and durability of the steel.
Enhanced corrosion resistance
While the protective life of galvanized coating is typically determined based on the total coating thickness, visually, the corrosion-free lifetime is more closely related to zinc thickness. Continuously galvanized steel products have a significantly thicker layer of free zinc, so they resist rusting and discoloration much longer than batch dip products.
Stronger galvanic protection
Compared to products that are cut from pre-galvanized metal, products that have been continuously galvanized and then formed have much smaller areas of exposed steel. Gregory Industries has conducted accelerated corrosion tests which confirm the continuous galvanizing process helps to reinforce edge strength and protect against wear and damage.
Improved coating ductility and adhesion
Batch dipped steel products are notoriously brittle and tend to crack when they are deformed or impacted. In contrast, a continuous galvanized coating is virtually 100% ductile free zinc. A continuous alloy-free coating can readily be bent nearly 180 degrees without cracking or peeling.
More environmentally friendly
Continuous galvanizing steel is environmentally friendly in terms of both lead content and energy usage. The lead content in our coatings falls within the RoHS (Restriction of Hazardous Substances) standards, and the total energy needed to galvanize in our facilities is at least three times lower than comparable galvanizing by the batch hot dip method.
Continuous galvanizing at Gregory Industries
Learn how our experienced team performs continuous galvanizing at our Canton, Ohio, manufacturing facility.Step 1: Cleaning
The steel coil is cleaned and prepped for galvanizing.
Step 2: Heating
Steel is heated to match the temperature of the zinc to ensure effective bonding.
Step 3: Coating
Zinc is applied using our custom air knives to ensure even application.
Step 4: Inspecting
All projects are meticulously tested to ensure all specifications and requirements are met.
Step 5: Cooling
The metal cools, and the zinc solidifies to create a strong metallurgical bond.
Step 6: Forming
Once the galvanizing process is complete, the steel is recoiled or roll formed into a finished product.
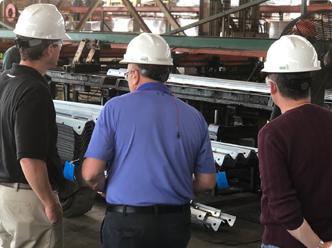
We take safety seriously. Our products save lives on roadways and worksites each day, and our employees deserve to feel safe and protected each time they enter our facilities.
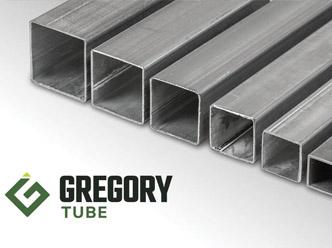
CANTON, Ohio — Gregory Industries announced today the launch of Gregory Tube, an evolution of its steel tube division, formerly known as Mid-Ohio Tubing.